Ethernet IP protocol explained for PLC communications
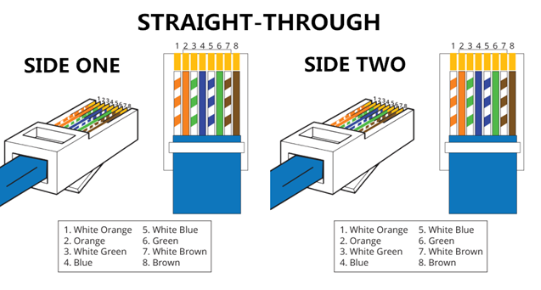
EtherNet/IP (IP = industrial Protocol)[1] is an industrial community protocol that adapts the common business Protocol (CIP) to standard Ethernet.[2] EtherNet/IP is one of the main industrial protocols in the usa and is broadly utilized in a number of industries inclusive of factory, hybrid and method. The EtherNet/IP and CIP technologies are managed via ODVA, Inc., a global alternate and standards improvement company founded in 1995 with over three hundred corporate participants.
EtherNet/IP makes use of both of the maximum broadly deployed collections of Ethernet requirements –the net Protocol suite and IEEE 802.3 – to outline the capabilities and features for its transport, network, statistics link and bodily layers. EtherNet/IP performs at level session and above (stage 5, 6 and 7) of the OSI version. CIP makes use of its object-orientated design to provide EtherNet/IP with the offerings and tool profiles wished for real-time manage packages and to promote regular implementation of automation features across a numerous ecosystem of merchandise. Further, EtherNet/IP adapts key elements of Ethernet’s wellknown capabilities and services to the CIP item model framework, along with the consumer Datagram Protocol (UDP), which EtherNet/IP makes use of to move I/O messages.
how ethernet works
In the field of Programmable Logic Controllers (PLCs), Ethernet cables commonly use the Ethernet/IP protocol. Ethernet/IP is an industrial protocol based on the standard Ethernet protocol, which is widely used for communication in computer networks.
Ethernet/IP is specifically designed for industrial automation applications and is built on two main components: Ethernet as the physical layer and the Common Industrial Protocol (CIP) as the application layer. CIP defines the message structure and services used for PLC communication.
The Ethernet/IP protocol provides a standardized way for PLCs and other industrial devices to communicate and exchange data. It allows devices from different manufacturers to communicate seamlessly by defining a set of rules and conventions. Some key features of Ethernet/IP in the PLC field include:
1. Real-Time Communication: Ethernet/IP supports real-time communication, allowing for precise and timely exchange of data between devices. This is crucial for applications that require tight synchronization or fast response times.
2. Device-Level Ring (DLR): Ethernet/IP supports DLR, a redundancy mechanism that ensures high network availability. DLR provides fault tolerance by creating a redundant ring topology, where data can flow in both directions, allowing for quick recovery in case of a network failure.
3. Message-Based Communication: Ethernet/IP uses a message-based communication model. Devices communicate by sending messages with specific formats, called CIP messages, which contain information such as data values, commands, or status updates.
4. Object-Oriented Data Model: Ethernet/IP follows an object-oriented data model, where data is organized into logical objects with attributes and services. This structure allows for a flexible and scalable approach to PLC programming and data exchange.
5. Integration with IT Networks: Ethernet/IP enables seamless integration between industrial automation systems and enterprise-level IT networks. It allows PLCs to exchange data with other devices, such as supervisory control and data acquisition (SCADA) systems, human-machine interfaces (HMIs), or enterprise resource planning (ERP) systems.
By utilizing the Ethernet/IP protocol, PLCs can leverage the benefits of Ethernet technology while ensuring reliable and efficient communication in industrial automation applications.
Ethernet/IP and TCP/IP are related but different protocols used in different contexts.
Ethernet/IP is an industrial protocol that operates at the application layer of the Ethernet protocol stack. It is primarily used in the field of industrial automation, including PLCs, to facilitate communication between devices and control systems. Ethernet/IP defines the messaging structure and services specific to industrial automation applications.
TCP/IP, on the other hand, is a suite of protocols that form the foundation of the internet and many computer networks. TCP/IP stands for Transmission Control Protocol/Internet Protocol and encompasses a set of protocols at various layers, including the network layer (IP), transport layer (TCP/UDP), and application layer (HTTP, FTP, SMTP, etc.). TCP/IP provides the rules and conventions for routing and transmitting data across networks.
While Ethernet/IP runs on top of Ethernet at the physical layer, data link layer, and network layer, TCP/IP operates at the network layer (IP) and transport layer (TCP/UDP) of the protocol stack. TCP/IP ensures reliable and ordered delivery of data packets between devices over an IP network.
In summary, Ethernet/IP is an application layer protocol used for industrial automation, while TCP/IP is a suite of protocols used for general networking, including internet communication. However, it’s worth noting that TCP/IP can be used as the transport layer protocol within Ethernet/IP for reliable data transmission when necessary.