Process automation to monitor ,control process plants
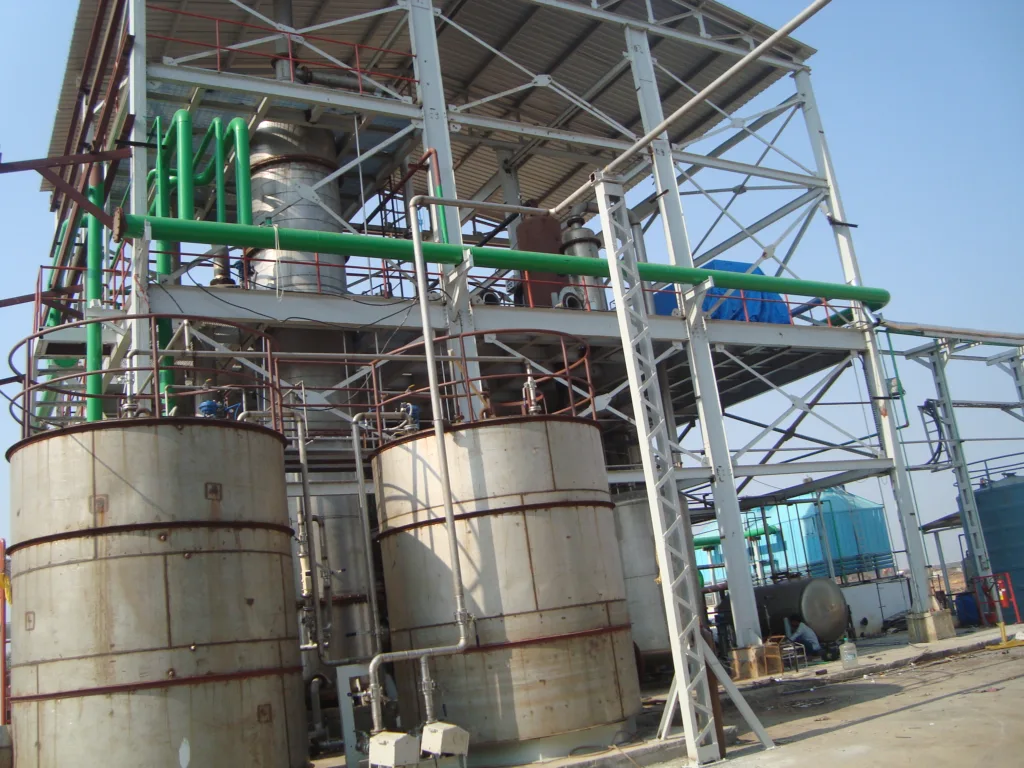
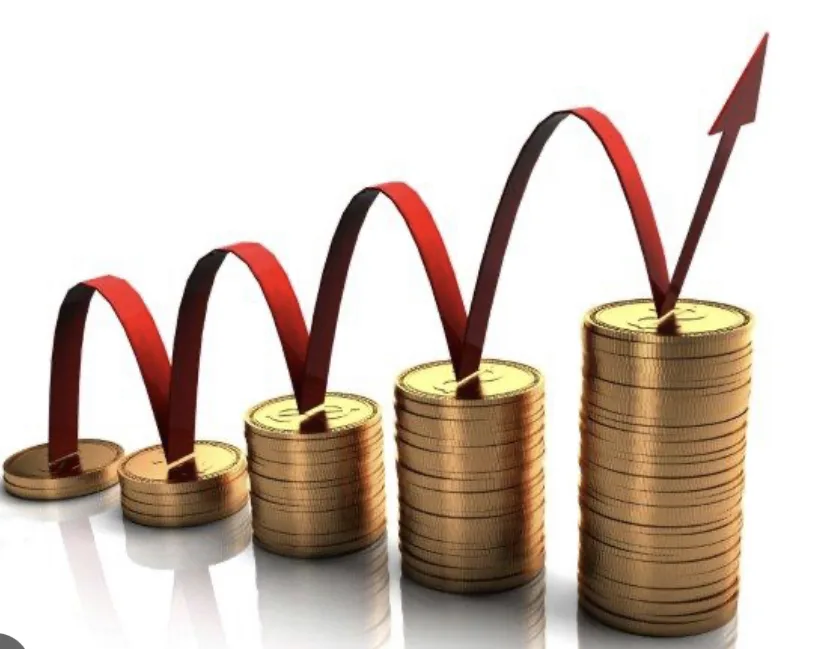
Advantages of Industrial Process Automation Systems
Industrial process automation is the utilization of technology to reduce human labor with automated workflows. It is a tech-driven solution that helps automate complex processes in different commercial sectors. The vital functions of process automation include automating processes, centralizing information, and reducing the requirement for input from people. With industrial process automation, companies, and business enterprises can reduce errors, remove bottlenecks, and neutralize data loss. It adds transparency and communication across every section with improved processing speed.
Working Standard Industrial Process Automation Systems:
- Finding automation potential
- Assessing & optimizing processes
- Defining executable procedures
- Designing forms & input masks
- Equipping for rollout
- Executing process automation
- Supervising results
- Finding an automatable process
- Discretizing actions
- Building a team, budget, and schedule
- Selecting controls hardware
- Defining automation goals
- Identifying the right solution
- Mapping out the process
- Incorporating the needs of the team
- Establishing KPIs
- Testing the automation
- Going live and monitoring the process
Process plant automation helps to save energy,make consistent product quality .
it’s achieved by carefully understanding the plant operations and designing engineering solutions to make the plant stable.
Flow control
In a proces plant the flow control as volume or mass is very critical to the process control usually its controlled against a Set Value and controlling with in 0.5% is considered good
Level- control
the level of the process vessels looks easy to common man but in the process plant when there is need to control the level with in 0.5mm which involves 250 litre of liquid and there are more then 3 factors controlling the level like inward flow,outward flow ,the evaporation and the Air ,the process become really challenging
Pressure Control
pressure is more of health measurement to the plant operation example is compressed air pressure or the steam pressure with in certain limits its non critical but outside the limit of 3 to 5% it’s variation becomes a problem to the stability of the plant.
Temperature control
Temperature in the process plant is one of the most critical parameter which shows the stability of the various process the more the temperature is stable better the plant is controlled
Process Automation advantages in chemical plants.
1. Enhanced Efficiency: Automation streamlines processes, reducing manual intervention and optimizing resource utilization. This leads to faster cycle times, increased productivity, and improved operational efficiency.
2. Consistent Quality: By precisely controlling process variables, automation ensures consistent output quality, minimizing variations and errors. This results in higher product reliability and customer satisfaction.
3. Improved Safety: Automation systems incorporate safety measures such as interlocks and alarms, reducing the risk of accidents. Operators can work in safer environments, protected from potential hazards.
4. Cost Savings: Automation optimizes resource usage, reduces energy consumption, minimizes waste generation, and lowers labor costs. Over time, this translates into significant cost savings for organizations.
5. Scalability and Flexibility: Automated systems can easily adapt to changing production requirements, accommodate new products or process modifications. This scalability and flexibility allow businesses to respond quickly to market demands and stay competitive.
6. Enhanced Data Analysis: Automation systems collect and store data, which can be analyzed to identify trends, optimize processes, and make informed decisions. Advanced analytics enable predictive maintenance and performance improvements.
7. Time Savings: Automation reduces manual tasks and streamlines processes, freeing up valuable time for operators and staff to focus on more complex or strategic activities.
8. Regulatory Compliance: Automation systems can enforce regulatory requirements and record process data, aiding in compliance audits and reporting obligations.
9. Improved Decision-making: Real-time monitoring and data availability through automation systems enable better decision-making. Managers can access critical information promptly and make informed choices to optimize processes and address issues promptly.
10. Competitive Advantage: By leveraging automation, organizations gain a competitive edge by increasing productivity, improving product quality, reducing costs, and responding swiftly to market dynamics.
In summary, process automation offers a range of benefits, including increased efficiency, consistent quality, improved safety, cost savings, scalability, flexibility, enhanced data analysis, time savings, regulatory compliance, better decision-making, and a competitive advantage in the market.
Process automation is a technology-driven solution that helps automate complex business processes in various industries, including chemical, oil and gas, pharmaceuticals, food and beverage, paper, mining, and cement. The key functions of process automation include automating processes, centralizing information, and reducing the requirement for input from people. By implementing process automation, businesses can remove bottlenecks, reduce errors and loss of data, and increase transparency and communication across departments, all while improving the speed of processing.
Process automation or automation systems (PAS) are used to automatically control a process, such as chemical plants, oil refineries, paper and pulp factories. These systems often use a network to interconnect sensors, controllers, operator terminals, and actuators. PAS is typically based on open standards, in contrast to a distributed control system (DCS), which is traditionally proprietary. The PAS is commonly associated with SCADA systems.
Process automation involves using sensors, actuators, computer technology, and software engineering to help power plants and factories operate more efficiently and safely. In the absence of process automation, plant operators have to physically monitor performance values and the quality of outputs to determine the best settings on which to run the production equipment. Maintenance is carried out at set intervals, resulting in operational inefficiency and unsafe operating conditions.
Process automation simplifies this by using sensors at thousands of spots around the plant to collect data on temperatures, pressures, flows, and other parameters. The information is then stored and analyzed on a computer, and the entire plant and each piece of production equipment can be monitored on a large screen in a control room. Plant operating settings are then automatically adjusted to achieve the optimum production, while plant operators can manually override the process automation systems when necessary.
Process automation systems typically consist of several components, including sensors, controllers, actuators, operator interfaces, and communication networks. These components work together to control and monitor the process, generating signals that are transmitted to the controller to make decisions about adjusting the process, communicating with the operator interfaces, and interconnecting the various components of the automation system.
Overall, process automation systems can help businesses to operate more efficiently, reduce costs, and improve safety by reducing the risk of human error.
Benefits of Process Automation in chemical industires
Industrial process automation refers to the use of technology and systems to control and monitor industrial processes, reducing manual intervention and increasing efficiency, accuracy, and productivity. It involves the integration of various hardware and software components to automate and optimize the operation of manufacturing or industrial processes.
The key elements of industrial process automation typically include:
1. Sensors and Actuators: Sensors are used to collect data on various process variables such as temperature, pressure, flow rate, level, and position. Actuators, on the other hand, are devices that control physical elements of the process, such as valves, motors, pumps, and conveyor belts. These sensors and actuators form the backbone of data collection and control within an automated system.
2. Programmable Logic Controllers (PLCs) or Programmable Automation Controllers (PACs): PLCs or PACs are the central control units in industrial automation systems. They receive input from sensors, process the data, and generate output signals to actuators based on a programmed logic. PLCs/PACs execute predefined instructions or algorithms to control the sequence, timing, and interlocking of various process components, ensuring that the process operates as intended.
3. Human Machine Interfaces (HMIs): HMIs provide a graphical or textual interface between operators and the automation system. They allow operators to monitor and control the process, providing real-time information, alarms, and status indicators. HMIs enable operators to interact with the automation system, set parameters, adjust settings, and respond to alerts or anomalies in the process.
4. Supervisory Control and Data Acquisition (SCADA) Systems: SCADA systems are used to monitor, control, and collect data from multiple remote sites or processes. They provide a centralized view of the entire industrial operation, allowing operators and managers to oversee and analyze the performance of various processes, identify trends, and make informed decisions. SCADA systems often integrate with PLCs, HMIs, and other data acquisition systems to gather and present data in a coherent manner.
5. Communication Networks: Industrial process automation relies on robust communication networks to facilitate the exchange of data between different components of the system. These networks can be wired (Ethernet, Fieldbus, etc.) or wireless (Wi-Fi, cellular, etc.). Communication networks enable seamless integration of various devices, enable remote monitoring and control, and facilitate data exchange between different levels of the automation hierarchy.
6. Data Logging and Analysis: Industrial process automation systems often include data logging capabilities to capture and store process data for further analysis, quality control, regulatory compliance, or troubleshooting purposes. Advanced analytics techniques can be applied to the collected data to identify patterns, optimize processes, detect anomalies, and improve overall system performance.
Ways to Implement Industrial Process Automation
- Survey the process
- Select practical tools
- Determine process requirements
- Establish control
- Automate the potential procedure
Why is Choosing Little Systems the Right Choice?
Specializing in PLC sequence logic for machine tool controls, we excel in diverse applications such as greenhouse automation and formaldehyde plant control. Our proficiency spans digital and analog input/output management, servo control, and communication protocols like Modbus and Can bus. Through integrating process instruments ranging from pressure to thermal mass flow meters, we achieve precise control with Cascaded PID tuning, ensuring accuracy within 0.03% of the set value. Monitored via SCADA every 5 seconds, our solutions guarantee reliable 24-hour operation.
FAQs
Automation using control systems to streamline industrial tasks.
Improved efficiency, quality, and safety; reduced costs.
Ensures consistency and real-time monitoring for quality assurance.
Initial costs, integration issues, cybersecurity, and skill requirements.
Automotive, pharmaceuticals, food, chemicals, and electronics.