Why Buy SCADA ?
SCADA is acronym for Supervisory Control & Data Acquisition
Genesis 64 is Mitsubishi Electric SCADA software
Genesis 64 Advanced Mitsubishi Electric SCADA software 223000 Indian Rupees onwards.
GENESIS64™ is a Mitsubishi electric SCADA software suite designed to facilitate machine control and monitoring in industries running on the computer.
With resources like hyper historian it can store the plant critical data It is compatible with Microsoft operating systems and seamlessly connects with various devices and databases, enabling system to collect and analyze data. This suite establishes communication between machines on the plant floor or building facilities and the company’s business systems. With a focus on efficiency and modern technologies, GENESIS64 offers a secure and intuitive kpi dashboard for visualizing and managing real-time data from manufacturing, energy with energy analytics , and business operations. It empowers operators, executives, and IT professionals to effectively monitor and control processes.
we at little systems have commissioned the prestigious projects of faridabad smart city where drinking water through out the city is distributed & monitored at Faridabad smart city Integrated control and command center .Telemetry remote devices monitor water treatment is also part of this project.All remote data is collated using internet over SIM cards from telemetry devices.
Scada is a PC software whose Licence needs to be purchased ,application development is the Process which needs to be customized all the TAG configuration using i/o map of PLC is done, User Interface is made by engineering team to make the User Experience so that the use of software becomes Easy & no alarms are missed & all important task of the operator are done with ease.
Scada Software when implemented looking into the plant requirements can be of immense help when features like Voice alarms ,historic trends ,data logging into excel reports & 2 screens are used to show the critical plant parameter along with their set values all the motor operations their selection running or tripping status is shown right poping up grabbing the operator attention.
With data reporting on the screen in datagrids & real time trending the minimum ,maximum and average value of the parameters are shown on screen without pressing any button the analysis of the plant operations can be further optimized & recorded with excel export of the data for the health monitoring & efficient running of the plant ,even the power usage and parameters are logged to maintain the check on the resources.
Historical trends are presented on the screen with selection on the screen to remove or add the no of pens shown in the historical trend by the operator without any configuration changes .
"Optimise your plant performance with xArrow SCADA .
Buy it for Just 35,000 INR! for 75 tags"
xArrow is easy to deploy and easy to use but very powerful SCADA software .It runs on Windows 11 and older windows versions. There is also a dedicated android version which can be used on android tablets or android mobile devices
Xarrow scada has built in features for process industry. It supports modbus protocol devices and can act as an OPC server, Modbus TCP slave, or Bacnet/IP gateway, enabling seamless integration with different systems. Whether you need a simple setup for a single operator or a complex setup with redundancy and multiple clients, xArrow can meet your requirements. Another convenient aspect is that you can access and browse the SCADA project using an Android phone. Moreover, xArrow is lightweight windows application which does not need DOT net and doesn’t need special Graphic cards or Xenon based PC hardware, such as powerful graphic cards, making it accessible to a wider range of employees.
at little systems we have commissioned over 150 projects on xarrow scada ranging from greenhouse automation to formaldehyde plant automation.all the field instruments are connected to SCADA through programmable logic controller.
Mitsubishi,Siemens,Omron,Delta ,IOT Modbus & other Communication Protocols default in Xarrow SCADA
This is how Xarrow SCADA Outshines competition SCADA software
- Organization can protect the process or machine set points by using multiple level password for operator ,supervisor login part of computer security.
- Support I/O server redundancy, system will switch to a backup server if the primary server failure
● Support historical and alarm server redundancy, if the primary server fails, the nodes get historical data and alarm from the backup server
● Support network redundancy, if Net A fails, system will switch to Net B
● Support station redundancy, if the primary station communication failure, the backup station will automatically start communicating
● Get station communication status by the corresponding system analog
● Node log in or log out can fire event
● Support archive historical data and alarm daily to a single data file
● All the information about write tag operation can be saved. - Ethernet cables are easy to use for data connectivity
More than 70 kinds of widgets, including text, 3D polyline, real-time data,
gauge, waterflow, data grid, historical trends, alarms, buttons, etc
● Support directly copy symbols in Symbol Factory and paste it into the drawing in
vector format
● Object-Oriented graphical interface ● Support 24 kinds of fill mode, including 16 kinds of color gradient
● Provide Undo/Redo function
● Support bitmap transparent, filling, scaling
● Support directly copy bitmap from other environment (such as a browser) and paste it into the project
● Support string search and replace function
● The running state of the real-time widget is decide by the given condition
● Directly edit the property of the sub-widget of a group widget without ungroup it
● Each widget can be configured with tooltip
● Support insert and configure the ActiveX
● Support 3D modal via xArrow plugin and DirectX technology
● Unlimited number of drawings, and the single screen sizes up to 10240*7680 pixels
● Each writeable widget and each drawing can be set the access permissions
● Support use the keyboard to simulate mouse messages, such as mouse move, mouse click, and click the [Tab] key can traverse all the
widgets in the drawing
All schematic of the plant can be easily designed using scada in built graphics tools
SCADA startup
● SCADA closed
● To a given time
● Periodically
● Tag’s alarm trigger
● Grouped alarm trigger
● Open the drawing
● Close the drawing
● Periodically when the drawing opened
● Hot key pressed in the drawing
● Mouse click down, click up or move on the widget
● When meet the condition of the time table
● Built-in HTTP server, no additional installation, easy to use
● Support non-standard HTTP port, such as 8080
● Support access web server in the LAN via router
● User be allowed to browse the site is configurable
● Whether to allow write tag’s value from browser is configurable
● By install web service at different node can let the user browse different part of system
● Can restrict user browse certain part of system by set the default drawing of web service
● Use Microsoft Internet Explorer can browse the project just as the native node
● User defined report template, a variety of widgets can be organized in one report
● Supports automatically or manually pagination, preview and print
● User defined page margin, header and footer
● Support direct access MS Excel report file
All the software development modules & widgets are designed in accordance with Windows operating habits, easy to use
● The design mode and the run mode can be opened simultaneously
● Integrated development workspace to manage the entire project, providing top-down design
approach
● Entire project data contained in one folder and its sub-folders
● Project manager can easily switch and import different project
● Simply configure the project by modify the default parameters, all changes are saved instantly
● Provide data import/export functions, users can use Microsoft Excel to build tags and structs of the
project
● Provide emulate PLC to simulating values of PLC variables
● Powerful gallery is user-friendly, and easy to create use’s own widgets
● Drawings can be imported/exported as the template
● Without compiling, all changes are WYSIWYG
● Script is easy to use, and easy to debug the error
Simple or complex data transfer logics can be written suing scripts
xArrow support Windows 7/8/10 /11
● Backward compatible with all the previous versions
● Easy to expand, including the protocol driver, the script commands, and the widget
● Alarm processing and preservation
● Support Client/Server mode, and support distributed data acquisition. All the real-time data and
historical data can be shared between different nodes
● Real time and multi-tasking kernel
● Provide redundant data acquisition and historical data processing
● Support xArrow’s own historical database and also supports Oracle, SQL Server, MySQL, Access or
PostgreSQL as its historical database server.
● Support use keyboard to simulate mouse click and movement message on the screen
● The drawings can be configured to adapt to different screen resolution
● Shipped with all the popular communication protocols free, and support OPC Client
● The project and all the needed modules can be packaged into one installation program
● Support project encryption/decryption
● Full Object Oriented technology
Built-in support for all the popular Programmable logic controllers (Siemens, GE, Schneider, Mitsubishi, Omron, Delta…, etc.), some of the inverter and some other
communication protocols
● Communicate via the serial port, TCP/UDP networks and other media
● Can be worked as the Modbus/Modbus TCP slave, and support write operation from Modbus/Modbus TCP master
● Can be worked as the DDE server and DDE client
● Build-in GraceMaster/GraceSlave protocol, support upload data from xArrow sub-station to xArrow central station
● Can be worked as OPC client and OPC server, and xArrow OPC server can be configured as writeable
● Access other database via ODBC interface
● Kernel use Hash algorithms to access real-time database
● Data acquisition and process using the event-driven mode
● Polling interval is configurable
● The write operation has higher priority level than the read operation
● Can specify a data to read
● Time-stamping of data with millisecond accuracy
Object-oriented data structures, including the station, string, analog and switch
● All the data forming a tree structure depend on the device it belongs
● Analog and switch can be configured as read-only or writeable
● Analog can be converted to physical values
● Analog support simple filtering function
● Analog has 5 alarm type, and have deadband concept.
● Switch has concept of 3 alarm type
● Alarm of the tag can be delayed to prevent false alarm, support used-defined alarm description,
voice alarm concept, Any alarms and can trigger script execution or play the prerecorded voice alarms.
● Use script to access all the information about the tag
● System analog show the time, alarm count and communication status of the system
● Audit trail for machine parameter change.
● Each user has a unique electronic signature
● User will be locked after a number of unsuccessful attempts
● User can manually logout or automatically logout after a period of inactivity
● Each log have a unique signature
● Option for double signature on doing operations
● Logging of previous value when change a value
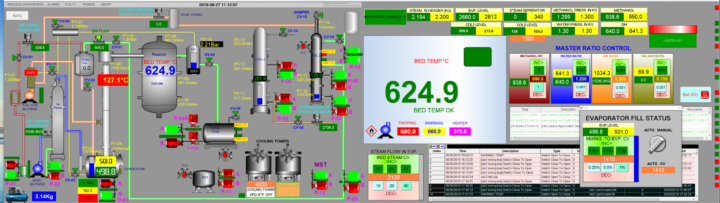

Scada for Industrial Automation. why? When? Where?
In industrial process automation, Scada is designed to accumulate data from several equipment, sensors, and devices throughout the facility. It offers real-time visibility and control over processes to operators. The industrial role of scada supports scada system price and those roles are,
Scada software collects data from several sensors, devices, and instruments. It transfers the data to a centralized interface that helps operators monitor temperature, flow rates, pressure, levels, and equipment status. Scada can control industrial processes, send alarms and notifications for events, past data storage and analysis, remote control & access, coordination with other systems, and security along with control on access.
SCADA (Supervisory Control and Data Acquisition) software plays a vital role in factory and process automation by providing a centralized system for monitoring, controlling, and managing industrial processes. It is designed to collect data from various devices, and equipment throughout a facility, enabling operators to have real-time visibility and control over the processes. Here are some key uses of SCADA system .
1. Real-time Monitoring: it collects data from multiple sensors, instruments, and devices, displaying it on a centralized interface. Operators can monitor critical process variables such as temperature, pressure, flow rates, levels, and equipment status in real-time. This allows them to identify anomalies, trends, or deviations from set points promptly, enabling proactive decision-making and timely intervention.
2. Process Control: it enables operators to control and adjust process parameters remotely or automatically. Through the software interface, operators can initiate or modify control commands that regulate actuators, valves, motors, or other equipment. This allows for precise control over the process, ensuring optimal performance and maintaining set parameters within desired ranges.
3. Alarming and Event Notification: it provide configurable alarm functionalities that notify operators of abnormal conditions, process deviations, or equipment failures. Alarms can be visual, audible, or sent via email or SMS notifications, ensuring operators are alerted to critical situations promptly. Operators can then take appropriate actions to resolve issues or initiate corrective measures, minimizing downtime and preventing potential disruptions.
4. Historical Data Storage and Analysis: it records and stores process data over time. This historical data serves as a valuable resource for analysis, performance evaluation, and troubleshooting. It allows operators to generate reports, trend charts, and statistical analyses to identify patterns, optimize processes, and improve overall operational efficiency.
5. Remote Access and Control: xarrow systems often support remote access, allowing authorized personnel to monitor and control processes from anywhere with an internet connection. This capability enables off-site monitoring, troubleshooting, and decision-making, enhancing operational flexibility and reducing response times.
6. Integration with Other Systems: it can integrate with various automation systems, including PLCs, HMIs, MES (Manufacturing Execution Systems), ERP (Enterprise Resource Planning) systems, and more. This integration allows for seamless data exchange, centralized control, and information sharing between different levels of the automation hierarchy. It enables higher-level decision-making, production planning, and data synchronization across multiple systems.
7. Security and Access Control: it incorporate security measures to protect against unauthorized access, data breaches, or malicious activities. User authentication, role-based access control, and encryption ensure that only authorized personnel can access and modify system settings, ensuring the integrity and confidentiality of data.
In summary, SCADA systems plays a crucial role in system automation by providing real-time monitoring, process control, alarming, data storage and analysis, remote access, integration with other systems, and security. It enables operators to efficiently manage and optimize industrial processes, ensuring operational efficiency, productivity, and safety.

SCADA (Supervisory Control and Data Acquisition) software plays a vital role in factory and process automation by providing a centralized system for monitoring, controlling, and managing industrial processes. It is designed to collect data from various devices, and equipment throughout a facility, enabling operators to have real-time visibility and control over the processes. Here are some key uses of SCADA system .
1. Real-time Monitoring: it collects data from multiple sensors, instruments, and devices, displaying it on a centralized interface. Operators can monitor critical process variables such as temperature, pressure, flow rates, levels, and equipment status in real-time. This allows them to identify anomalies, trends, or deviations from set points promptly, enabling proactive decision-making and timely intervention.
2. Process Control: it enables operators to control and adjust process parameters remotely or automatically. Through the software interface, operators can initiate or modify control commands that regulate actuators, valves, motors, or other equipment. This allows for precise control over the process, ensuring optimal performance and maintaining set parameters within desired ranges.
3. Alarming and Event Notification: it provide configurable alarm functionalities that notify operators of abnormal conditions, process deviations, or equipment failures. Alarms can be visual, audible, or sent via email or SMS notifications, ensuring operators are alerted to critical situations promptly. Operators can then take appropriate actions to resolve issues or initiate corrective measures, minimizing downtime and preventing potential disruptions.
4. Historical Data Storage and Analysis: it records and stores process data over time. This historical data serves as a valuable resource for analysis, performance evaluation, and troubleshooting. It allows operators to generate reports, trend charts, and statistical analyses to identify patterns, optimize processes, and improve overall operational efficiency.
5. Remote Access and Control: xarrow systems often support remote access, allowing authorized personnel to monitor and control processes from anywhere with an internet connection. This capability enables off-site monitoring, troubleshooting, and decision-making, enhancing operational flexibility and reducing response times.
6. Integration with Other Systems: it can integrate with various automation systems, including PLCs, HMIs, MES (Manufacturing Execution Systems), ERP (Enterprise Resource Planning) systems, and more. This integration allows for seamless data exchange, centralized control, and information sharing between different levels of the automation hierarchy. It enables higher-level decision-making, production planning, and data synchronization across multiple systems.
7. Security and Access Control: it incorporate security measures to protect against unauthorized access, data breaches, or malicious activities. User authentication, role-based access control, and encryption ensure that only authorized personnel can access and modify system settings, ensuring the integrity and confidentiality of data.
In summary, SCADA systems plays a crucial role in system automation by providing real-time monitoring, process control, alarming, data storage and analysis, remote access, integration with other systems, and security. It enables operators to efficiently manage and optimize industrial processes, ensuring operational efficiency, productivity, and safety.
How does Scada Operate?
Sensors register measurements and send data to programmable logic controllers and remote terminal units. RTUs gather data from sensors and transmit commands to control relays. Programmable logic controllers control operational equipment in industrial processes. Scada combines the data accumulated from PLCs and RTUs to generate visual representation and transmit commands to centralized locations.
Industrial Advantages of Scada
Scada is a computer-based system that offers a plethora of advantages such as preventing & troubleshooting problems, remote accessibility, reduced downtime, decreased energy costs, exercise improvement in processes, connection with valves, motors, and sensors with HMI software, reduced response time, and control industrial process using a remote interface or through local means.
Why Choose Little Systems for Scada?
Welcome to our team of experienced engineers, having a collective 90 years of automation experience. We adeptly navigate the complexities of PLC SCADA panel design, satisfying stakeholders like fabricators, consultants, site conditions, and our team. From panel assembly challenges to site commissioning hurdles, we ensure seamless operations. With expertise in PLC sequence logic, process automation, and SCADA controls, we offer reliable solutions tailored to your budget, addressing pain points within your budget and application constraints.
FAQs
SCADA stands for Supervisory Control and Data Acquisition.
Yes, SCADA does support the MQTT protocol for IIoT
SCADA pricing depends on factors such as the number of tags and additional functionalities selected.
It’s preferred to use a professional-class workstation PC for running SCADA software.
SCADA can serve as an alarm system, facilitate security management, and generate reports for analyzing plant performance and operations.
PLC is a hardware component, unlike SCADA, which is a software running on the computer or an android device.
No, SCADA licenses are sold with perpetual licensing.
SCADA provides specific functions to specific users through a login process, enhancing security management.
The primary distinction is that PLC is hardware, while SCADA is software.
Yes, SCADA offers the capability to generate reports through its user interface for analyzing plant performance over certain periods.