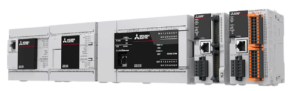
Factory Automation solutions to make plant efficient

PLC
We have been suing PLC in Factory automation since last 30 years in various Machine starting from very simple machine like Washing Machine to Critical ovens
SCADA
SCADA systems are gaining more and more popularity in todays times as the need for Quality improves in the automotive sector and traceability needs are required
Control Panels
Control Panels are made in after understanding the needs of the customer in technical as well as budget they are designed , assembled and commissioned at site
Servo
Servo systems are used where precision in positioning needs are required apart from that when two or more axis have to work together advanced control for the motion control are used
VFD
VFD systems are used to control the speed of induction motor for conveyors ,pumps etc apart form the speed control they are also helpful in energy conservation
Industrial automation replaces human efforts and errors by utilizing control systems and information technologies to manage various industrial processes and types of machinery. The procedure is designed to increase manufacturing quality and enable process flexibility. With high productivity, quality, safety, flexibility, and information accuracy, industrial automation is an inevitable factor for companies seeking long-term success. Programmable Logic Controllers (PLCs) and Supervisory Control and Data Acquisition (SCADA) systems are two key elements in the industrial automation process. PLC SCADA provides concurrent control and comprehensive supervision of multiple industrial operations.
Programmable Logic Controllers have played a crucial role in factory automation for the past three decades, enabling the efficient and reliable control of various machines, from simple appliances like washing machines to complex and critical systems, such as ovens. A programmable logic controller, or PLC, is a mini-industrial computer used to control electromechanical processes. The logic behind their creation is to monitor the state of input devices and make decisions based on a customized program that controls the state of output devices. Programmable logic controllers are made of input points, output points, and a central processing unit. The PLC in industrial automation operates as a single unit that can be used for process monitoring, enforcing process automation, and specifying machine functions. Let’s delve into the details of their applications in these machines.
1. Washing Machines:
Washing machines are a standard industrial machine that relies on them for automation. It controls the entire washing process, including water inflow, temperature regulation, drum rotation, detergent dispensing, and timing. The PLC executes a programmed sequence of operations, ensuring the correct cycle is followed based on user input or preset settings. It also monitors various sensors, such as water level sensors, temperature sensors, and door interlocks, to ensure safe and efficient operation.
2. Ovens:
They find extensive use in controlling industrial ovens, including those used in food processing, baking, curing, or heat treatment applications. They provide precise temperature control, heating/cooling cycle management, and safety monitoring. Temperature sensors inside the oven relay information to them, which in turn adjust the heating elements or gas burners to maintain the desired temperature. They also monitor parameters like exhaust gases, pressure, and safety interlocks to ensure safe operation and prevent accidents.
The advantages of using it in both washing machines and ovens are numerous:
1. Flexibility: It offers a high degree of flexibility, as it can be easily reprogrammed and reconfigured to accommodate different washing cycles or oven recipes. This adaptability enables manufacturers to introduce new features or modify processes without requiring significant hardware changes.
2. Reliability: They are designed for industrial environments, offering robustness and reliability. They are capable of operating in harsh conditions, including high temperatures, humidity, and electrical noise, making them suitable for factory automation applications.
3. Ease of troubleshooting: It simplifies the troubleshooting process through its modular design. Faulty components can be easily identified and replaced, minimizing downtime and maintenance costs.
4. Safety: It incorporates safety features such as emergency stop circuits, interlocks, and fault detection mechanisms. These ensure that machines operate within predefined safety limits, protecting both the equipment and operators.
5. Integration: It can integrate with other automation systems, such as Human-Machine Interfaces (HMIs), Supervisory Control and Data Acquisition (SCADA) systems, and enterprise-level networks. This integration enables centralized control, data logging, and remote monitoring of machines.
Over the past three decades, its technology has undergone significant evolution, with advancements in processing power, memory capacity, communication capabilities, and programming tools. These developments have further enhanced the capabilities and applicability of it in factory automation, enabling more efficient, accurate, and intelligent control of machines.
It’s worth noting that while they have been widely used in factory automation, other technologies such as programmable automation controllers (PACs) and industrial PCs are also gaining prominence, offering additional functionalities and performance in specific applications
Supervisory Control and Data Acquisition(SCADA):
SCADA is an integration of software & hardware designed to help users control industrial operations both in a physical state and through remote access. It supervises and analyzes real-world data, controls equipment and monitors equipment conditions, accumulates, processes & records data, and helps automate control processes of industrial automation. Scada automation companies operate in the manufacturing, civil engineering, and construction domains.
The business advantages of using Scada are huge. Proactive maintenance, safety, remote supervision & control, security, predictive analysis, enhanced efficiency, etc are among the few.
Scada systems integrated with industrial devices can monitor and control operational processes that can improve response time & accuracy. The integration of scada plc systems can enable data sharing and establish communications between various devices and procedures. Scada systems improve efficacy and quality through production strategy synchronization, inventory, and maintenance schedules using data stored in these systems.
Enhancing Efficiency and Precision: The Vital Role of Them and SCADA in the Machine Tool Industry
In the dynamic landscape of the machine tool industry, precision, efficiency, and automation are paramount. To meet these demands, Programmable Logic Controllers and Supervisory Control and Data Acquisition (SCADA) systems have emerged as indispensable tools. PLCs and SCADA solutions work in harmony, enabling the automation, control, and monitoring of complex machine tool processes. In this article, we will examine the importance of SCADA technology, highlighting its crucial roles in enhancing productivity, accuracy, and operational excellence in the machine tool industry.
1. Automation and Control :
PLCs are the backbone of automation in the machine tool industry. With their ability to control various machine functions, including motion control, speed regulation, and tool changes, they streamline operations and minimize manual intervention. They serve as the central control unit, executing programmed instructions and managing the overall performance of the machine. By harnessing PLCs, machine tool manufacturers achieve consistent, reliable, and repeatable processes, resulting in improved quality, reduced downtime, and increased productivity.
2. Real-time Monitoring and Data Acquisition :
SCADA systems complement PLCs by providing real-time monitoring and data acquisition capabilities. SCADA software collects data from PLCs and other connected devices, enabling operators to visualize and analyze critical process variables. By presenting real-time insights, SCADA empowers decision-makers to identify potential issues promptly, optimize machine tool performance, and make data-driven improvements. SCADA also facilitates data logging, historical analysis, and the generation of comprehensive reports for performance evaluation and process optimization.
3. Fault Diagnosis and Maintenance :
PLC and SCADA technologies play a pivotal role in fault diagnosis and maintenance strategies. PLCs constantly monitor machine tool parameters, sensor readings, and system performance. In case of deviations or malfunctions, PLCs trigger alarms or safety measures to prevent further damage. Simultaneously, SCADA systems capture and display these alarms, allowing operators to take prompt corrective actions. By enabling early fault detection and timely maintenance, PLCs and SCADA solutions contribute to minimizing machine downtime, reducing repair costs, and extending the lifespan of equipment.
4. Flexibility and Adaptability :
The machine tool industry requires adaptability to accommodate various production requirements. PLCs offer immense flexibility through their programmable nature. Manufacturers can easily modify PLC programs to accommodate different machine tool setups, varying product specifications, or changes to the production line. This agility ensures swift reconfiguration, reduced setup times, and improved overall equipment effectiveness (OEE). SCADA systems further enhance flexibility by providing intuitive user interfaces that enable operators to make adjustments, set parameters, and monitor processes efficiently.
5. Enhanced Safety and Risk Mitigation :
Machine tool operations inherently involve risks, including potential accidents and material damage. PLCs and SCADA systems play a crucial role in enhancing safety and mitigating risks. PLCs implement safety protocols, such as emergency stop functionalities, interlocking mechanisms, and safety interlocks to prevent hazardous situations. SCADA systems monitor safety conditions, display warning messages, and facilitate emergency response procedures. By integrating these technologies, machine tool manufacturers can ensure a safer working environment, comply with regulatory standards, and protect both personnel and assets.
6. Scalability and Integration :
As machine tool businesses evolve, scalability and integration become crucial factors. PLC and SCADA solutions offer seamless scalability, enabling the addition of new machines, expanded production lines, or integration with enterprise resource planning (ERP) systems. PLCs can communicate with multiple devices, including human-machine interfaces (HMIs), motor drives, sensors, and actuators, while SCADA systems provide a unified interface for controlling and monitoring these interconnected components. This synergy ensures efficient information exchange.
Mitsubishi: The Ideal Choice for Machine Tools and Suitable PLC Solutions
When it comes to machine tools, precision, reliability, and efficiency are paramount. Mitsubishi Electric has established itself as a leading provider of automation solutions, offering a wide range of programmable logic controllers (PLCs) that are specifically designed to meet the demands of the machine tool industry. In this article, we will explore why Mitsubishi is a top choice for machine tools and how their PLC solutions are well-suited for this sector.
1. Expertise in the Machine Tool Industry :
Mitsubishi Electric has extensive expertise and a deep understanding of the machine tool industry. With decades of experience, they have developed a comprehensive range of automation solutions tailored to the specific needs of this sector. This industry knowledge enables Mitsubishi to provide PLCs that seamlessly integrate with machine tools and deliver optimal performance.
2. High Performance and Precision :
Machine tools require precise control and high-performance capabilities, and Mitsubishi PLCs excel in these areas. Mitsubishi offers PLCs with fast processing speeds, high-resolution analog input/output modules, and advanced motion control functionalities. These features ensure accurate positioning, smooth operation, and tight synchronization of machine tool movements. With Mitsubishi PLCs, machine tool manufacturers can achieve exceptional precision, resulting in improved product quality and reduced scrap rates.
3. Robust and Reliable :
Machine tool applications often involve harsh operating conditions, including vibrations, temperature variations, and exposure to dust and debris. Mitsubishi PLCs are designed to withstand these challenging environments, offering rugged construction and high resistance to electrical noise. They are built to deliver reliable performance, even in demanding situations, ensuring uninterrupted operation and minimal downtime for machine tools. This reliability is crucial for maintaining productivity and meeting production deadlines.
4. Scalability and Flexibility :
Machine tool manufacturers need solutions that can adapt to evolving production requirements. Mitsubishi PLCs offer scalability and flexibility, allowing easy expansion and integration with existing systems. With Mitsubishi’s modular PLC architecture, additional input/output (I/O) modules can be added or removed as needed, accommodating changing machine tool setups. The PLC programming software provides a user-friendly environment, facilitating quick program modifications and system reconfigurations. This scalability and flexibility allow machine tool manufacturers to optimize their processes, improve efficiency, and respond effectively to market demands.
5. Comprehensive Support and Services :
Mitsubishi Electric is known for its excellent customer support and comprehensive services. They provide extensive technical documentation, training programs, and online resources to help machine tool manufacturers effectively implement and maintain their PLC solutions. Mitsubishi’s global network ensures prompt and reliable support, ensuring minimal disruptions to production operations. Additionally, Mitsubishi offers software tools for PLC programming, monitoring, and troubleshooting, enabling efficient development and debugging of machine tool applications.
Difference Between PLC and SCADA
The primary difference between PLC and SCADA is that PLC is a hardware-based system, while SCADA is a software-based system. PLC has a physical existence that can be checked for any irregularities, and SCADA is a computer-operated software that shares similarities with an operating system. The primary purpose of the PLC design is to control tasks, devices, and/or processes on a small scale. SCADA is designed to offer superior-level monitoring, data acquisition, and analysis of industrial processes. SCADA has more capability compared to PLC. Programmable logic controllers can execute operations at the machine and equipment level. SCADA provides a comprehensive view of the industrial process through visualization, data acquisition, and monitoring. PLC and SCADA play crucial roles in industrial automation, and both systems are designed for specific reasons and with a particular logic.
Expertise in Little Systems in PLC, SCAD, and Industrial Automation
We’re experts in crafting PLC sequence logic for machine tool controls and tailoring automation solutions to meet the specific needs of various industries. From greenhouse automation to managing complex formaldehyde processes, we’ve excelled in handling complex industrial needs. We integrate third-party devices using multiple communication protocols, such as Modbus and CAN bus. Additionally, we’re skilled in fine-tuning cascaded PID controllers for precise control over flow, level, pressure, and temperature. We aim to ensure accuracy and reliability, with every detail monitored through SCADA systems. Our expertise lies in providing industry-grade PLC and SCADA systems to clients, as well as prompt industrial automation solutions.
Mitsubishi Electric has established itself as a trusted provider of PLC solutions for the machine tool industry. Their expertise, high-performance capabilities, reliability, scalability, and comprehensive support make Mitsubishi PLCs an ideal choice for machine tool manufacturers. By leveraging Mitsubishi’s PLC solutions, machine tool manufacturers can achieve enhanced precision, productivity, and operational efficiency, ultimately leading to improved competitiveness in the market.
FAQs on PLC SCADA Automation
Its full form is supervisory control and data acquisition.
Yes, it does support MQTT protocol for IIOT.
It’s a software system that is a program running on pc and is connected to the controller. Scada engineering is done to monitor and analyze the plant data.
PLC is a hardware component, whereas SCADA is a software component
The price changes as per the number of tags in most cases, but also with functionality like energy module or statistical module selected with few vendors.
It is preferred to use a professional class workstation PC.
Scada can perform the task of an alarm system to direct the attention of the operator to processes going out of limits.
Scada can also facilitate security management. It provides specific functions to specific users through the process of Login
No usually scada sells with a perpetual license.