PLC vfd control panels
Formaldehyde Plant PLC VFD Panel
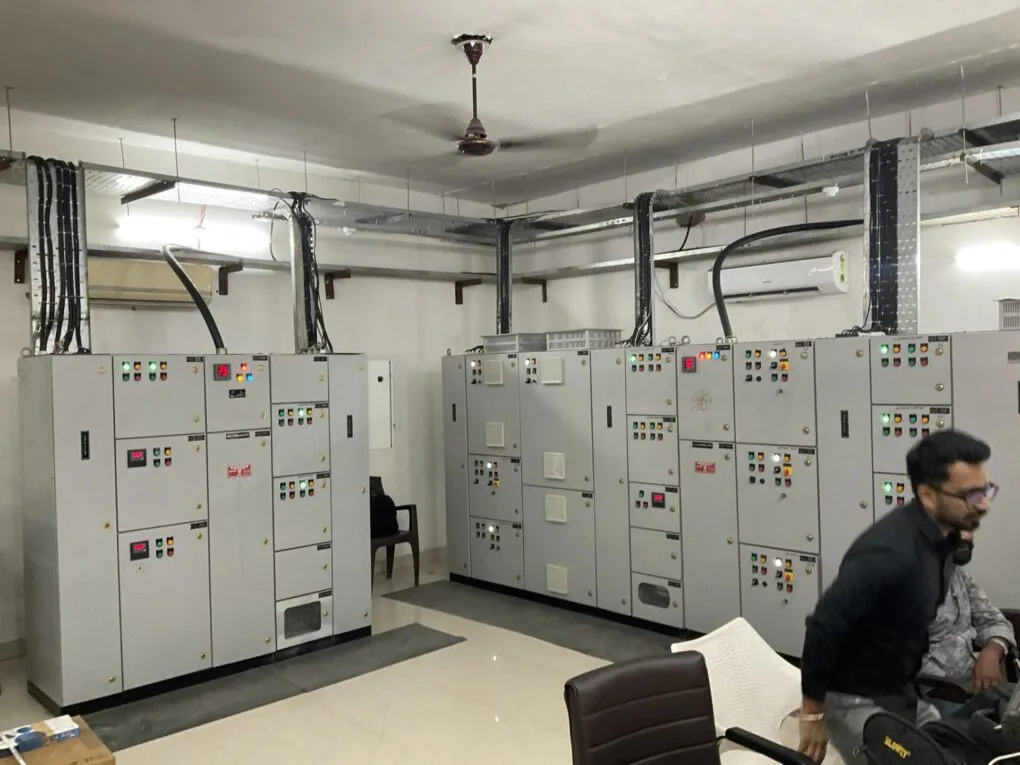
PLC VFD Panel scope of Automation
- Controls all electrical Pump motors ON/OFF/Alarms
- Monitors the motors electrical Circuit breakers for ON/OFF or trip status.
- Control & protects all electrical VFD for blowers ,Pumps, cooling tower Fans etc
- Control the Process PID for various Flow loops controls
- formaldehyde plant has critical PID loops being controlled through Mitsubishi process plc.
- Control the levels of evaportator ,Steam separator, Mixing tank & absorption columns
- Possibility to run designated pumps on VFD or On DOL
- SCADA integration of RO water treatment plant ,electrical Energy meters
- Pressure monitoring of all the plant points 21
- Temperature monitoring of various points 23
- Warning – trip alarms for the reactor bed temperature.
- Programming logic controller of Mitsubishi electric IQR series is used for process control and logic control of motor control center.
- electrical current ,voltage of all VFD driven motors are monitored on SCADA.
- All instrumentation signal are connected to SCADA through panel.
- Uses Control relay to switch contactors, valves etc
- this panel incorporates mitsubishi PLC
- Panel video from the process plant site.
This Panel does following operations

PLC panel for sheet metal power press control & automation.
- Main motor star delta operations through relays
- Shut height adjustment through motor control
- Two hand operations control for operator safety
- Foot switch operations
- Programmable logic controller of Mitsubishi Electric is used to control machine operations.
- Top stop function through proximity switches & PLC
- Pneumatic pressure interlock for low pressure alarm
- many other safety interlocks like Light curtains lubrication level and operations
- We use RITTAL Enclosures for dust protection.
- GS2107 GOT simple ,7″ touch hmi is used to display the production and interlock safety
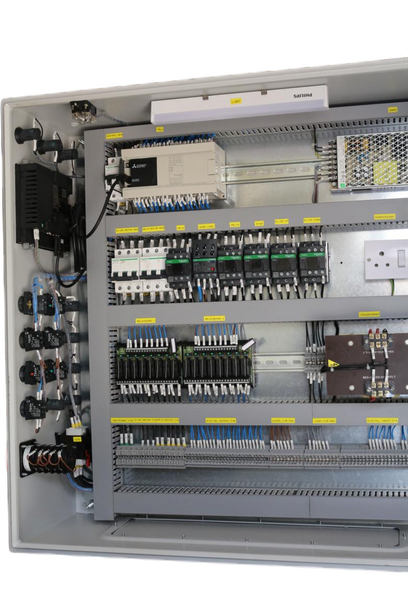

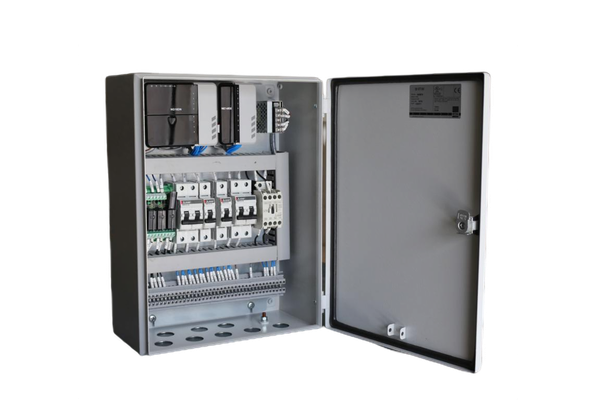
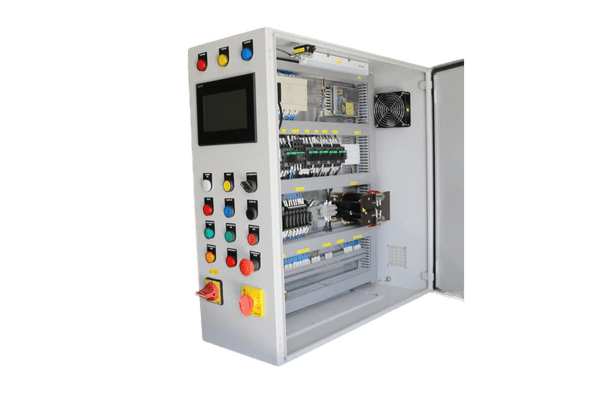
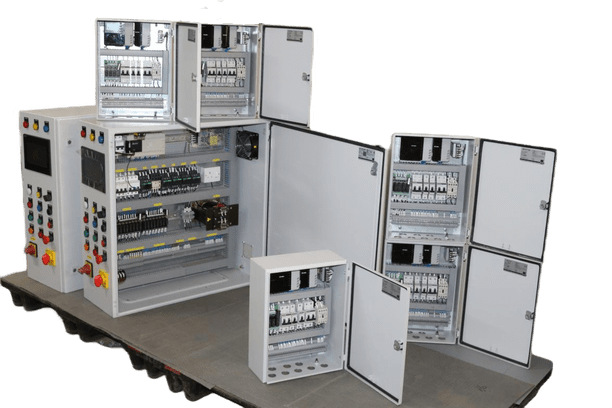
VFD panels
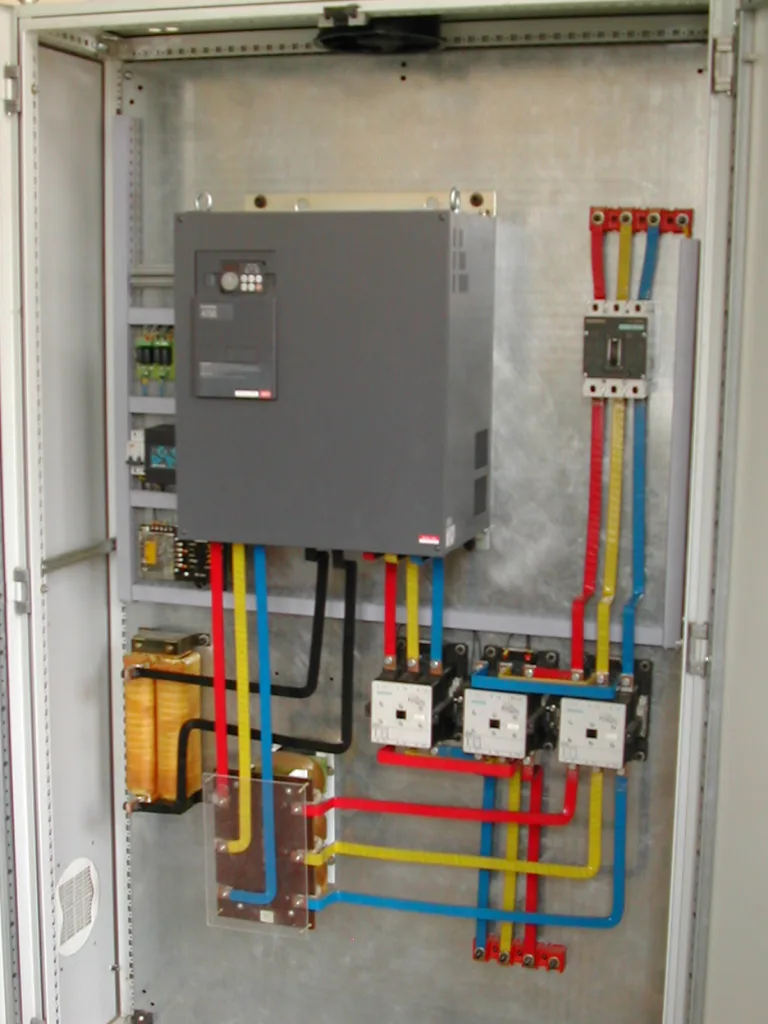
Mitsubishi Vfd for automation of compressor motor control.
the had to control the compressor motor RPM so as to deliver near constant pressure of 6bar irrespective of the Manufacturing load variation running with in the plant at different times of the work shift timing .
Mitsubishi VFD has some special capacitors for long life and has on site repairs above 50 HP
especially control was useful for energy conservation during lunch or tea time when the requirement of the commpressed air with in the plant dropped at this time the the motor RPM automatically dropped making the pressure under the set point .
without the PID action where RPM is the increased or decreased to maintain the compressed air line pressure.
Importance of Reliable PLC panels
Understanding PLC Panels ,prices & specifications
Programmable logic controller panels are undersized solid-state computers. They are programmed with customized instructions to execute distinctive tasks. PLCs are used in various industrial sectors for industrial control systems. Their function is to run processes and control machines, for example, assembly lines, robotic devices, process fault diagnosis, etc. The implementation of PLC is to ensure control of system functions using the internal logic embedded within. PLCs monitor the state of the input devices and generate decisions based on custom programming to regulate the state of output devices.
Working Principle of a PLC Control Panel
The working principles of a PLC control panel are as follows,
- The CPU supervises input status and analyzes the information received.
- After the assessment, the CPU follows instructions programmed in the PLC software and determines the next step.
- The CPU controls the output.
- The instructions dictate to repeat the task in a loop.
Components of a PLC Control Panel
The parts and devices inside a programmable logic controller are mentioned below:
- Processor or CPU (Central Processing Unit)
- Memory modules (RAM and ROM) (Most PLCs have them inbuilt into the CPU)
- Analog Input modules
- Digital Input modules
- Analog Output modules
- Digital Output modules
- Communication modules (Ethernet, RS-232, RS-485, etc.)
- Power supply module
- Programming software
- Programming cables
- Programming devices (HMI, handheld programmers, etc.)
- Terminal blocks
- Mounting racks or bases
- I/O connectors
- Expansion modules
- High-speed counters and timers (Hardware/Software)
- Proportional-Integral-Derivative (PID) controllers
- Motion controllers
- Data logging modules
- Safety modules
- Redundant processors and power supplies
- Remote I/O modules
- Distributed I/O modules
- Human-machine interface (HMI) devices
- Barcode scanners
- RFID (Radio-Frequency Identification) readers
- Vision sensors
- Servo drives and motors
- Stepper drives and motors
- Linear encoders
- Safety relays
- Push buttons and indicator lights
- Limit switches
- Temperature sensors
- Signal conditioners
- Signal isolators
- Operator panels
- Industrial PC
- Industrial Ethernet switches
- Encoders
- Solid-state relays
- Isolation amplifiers
- Cooling Fans
Advantages of PLC Control Panel
PLC control panels offer various significant advantages. Some of them are discussed below,
- Reliability:-
PLC will run with zero degradation over time after the software is written, debugged, and tested. This is why, PLC-operated systems offer more reliability than the rest.
- Communication:-
PLC provides remoter monitoring and the data received can be transmitted to a centralized location.
- Cost Reduction:-
After the installation and successful execution of the system, PLCs are not required to be rewritten under any circumstances.
Little Systems on PLC SCADA Control Systems & Scada Control Panel
Little Systems offers customized plc control panels for their clients. It includes a Formaldehyde Plant Panel, a Mitsubishi PLC panel for Power press control, a bottle-crushing machine panel, etc incorporating motor control ,circuit breaker ,relays & ladder logic control.
What Makes Our PLC Panels Better?
With over 30 years of experience, we specialize in crafting top-notch PLC control panels for various industries, from machine tools to formaldehyde plants. Our tailored solutions optimize performance and precision, ensuring seamless operations. We excel in automotive production lines, integrating efficient Andon systems for enhanced productivity. Our expertise extends to intricate formaldehyde plant controls, prioritizing safety and compliance. Count on us for unparalleled excellence, reliability, and personalized service to meet your unique needs. Trust us as your ultimate partner for PLC control panels
“30 Years of Expertise in PLC Control Panels for Machine Tools to process plants likeFormaldehyde Plant “
Our extensive experience spans three decades, during which we have honed our skills in designing, fabricating, and assembling top-quality PLC control panels. Our expertise extends across diverse industries, allowing us to cater to a wide array of applications. From simple machine tools to complex cut-to-length machines, we have successfully delivered tailor-made control panels that optimize performance and precision.
Our proficiency extends beyond manufacturing processes to automotive production lines, where we have implemented highly efficient Andon systems. These systems ensure seamless communication and real-time monitoring, contributing to improved productivity and fault detection in automotive assembly.
Moreover, our capabilities extend to intricate formaldehyde plant controls. By leveraging our comprehensive knowledge, we design and construct control panels that uphold the rigorous demands of this industry, ensuring optimal performance, safety, and compliance.
With our three-decade track record, we have garnered invaluable expertise, allowing us to provide unparalleled solutions to meet the unique requirements of each client. Our commitment to excellence, precision, and reliability makes us the ideal partner for all your PLC control panel needs.
PLC (Programmable Logic Controller) panels are an essential component in factory and process automation systems. They play a vital role in monitoring, controlling, and coordinating various processes and equipment within an industrial environment. Here are some reasons why PLC panels are crucial:
1. Control and Automation: PLC panels serve as the central control hub for automating and controlling machinery, equipment, and processes in a factory. They receive input signals from sensors and other devices, process the information based on programmed logic, and generate output signals to actuate actuators and devices. PLC panels enable precise and reliable control of complex automation sequences, ensuring consistent and efficient operation.
2. Process Monitoring and Visualization: PLC panels provide real-time monitoring and visualization of processes.
3. Sequence and Logic Control: PLC panels excel in executing programmed logic and sequential control. They can manage complex processes by defining logical relationships, conditions, and sequences of operations. PLC panels enable the automation of tasks that involve multiple devices, sensors, and actuators, ensuring accurate and synchronized operation.
4. Data Acquisition and Processing: PLC panels facilitate data acquisition from various sensors and devices. They can collect data on process variables, equipment status, and production metrics. PLCs can also process this data in real-time, perform calculations, implement control algorithms, and generate reports. The acquired data helps in process optimization, predictive maintenance, and decision-making.
5. Communication and Integration: PLC panels support communication protocols that allow seamless integration with other automation systems, devices, and networks. They can exchange data with supervisory control and data acquisition (SCADA) systems, manufacturing execution systems (MES), enterprise resource planning (ERP) software, and other control devices. PLC panels enable centralized control and coordination of different automation components and systems.
6. Fault Detection and Safety: PLC panels provide advanced diagnostic and fault detection capabilities. They can monitor system parameters, detect anomalies, and trigger alarms or shutdown procedures in case of safety hazards or equipment malfunctions. PLC panels contribute to enhancing operational safety and reducing the risk of accidents in industrial environments.
PLC panels are a critical component in factory and process automation, enabling efficient, reliable, and intelligent control of industrial processes. Their ability to monitor, control, and integrate various components and systems contributes to improved productivity, quality, safety, and overall operational efficiency in manufacturing environments.
Enclosure we use in PLC panels
PLC panels for following clients & appplications
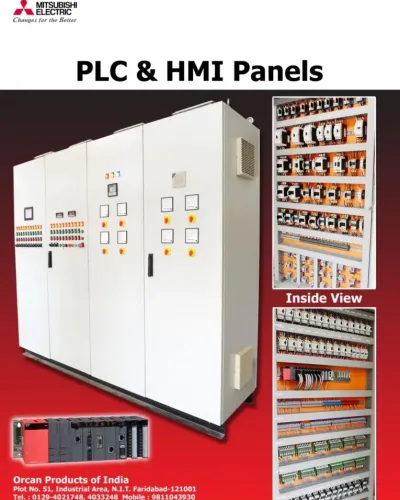
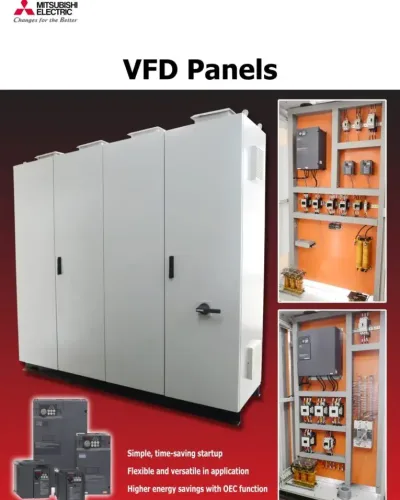
FAQs
By following industry standards such as NFPA 79 and implementing redundant systems where necessary.
Analyzing error codes, conducting thorough inspections, and utilizing diagnostic tools like PLC programming software.
Proficient in designing and configuring HMIs to interact seamlessly with PLC systems for user-friendly control.
Attending seminars, participating in online forums, and regularly reading industry publications to stay informed.
enclosure specifications do matter as the IP ratings where adhered to by quality enclosure manufacturers like rittal