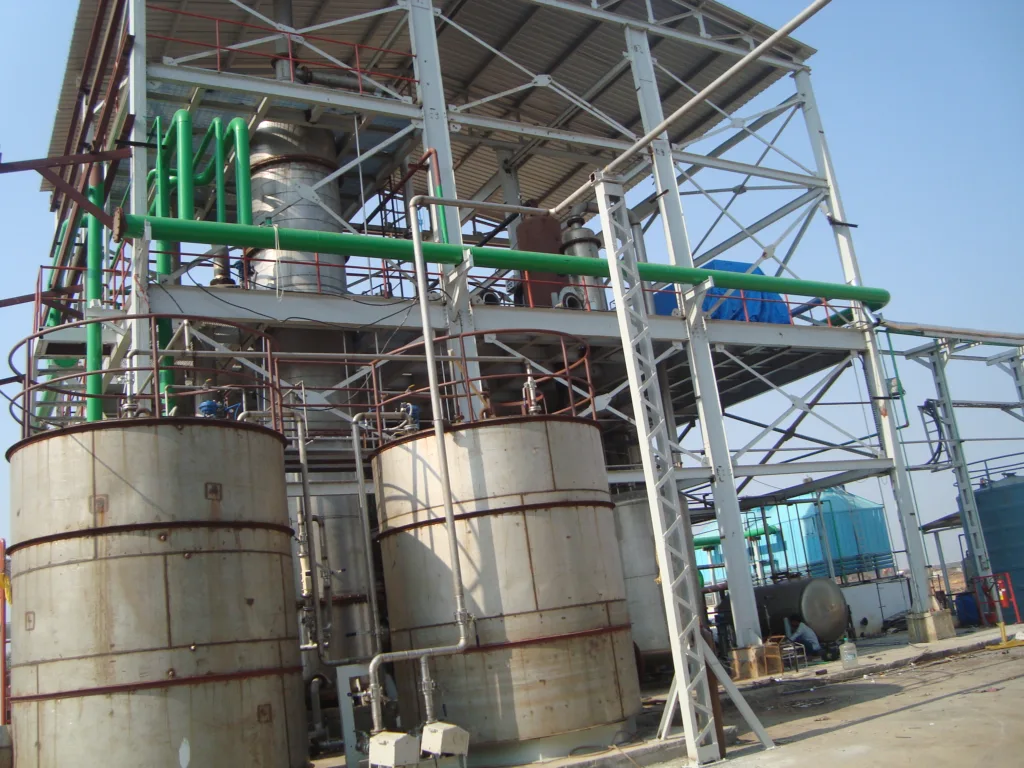
Process plant Instruments
Process instruments play a key role in controlling plant
Massflow meter
A mass flow meter, also referred to as an inertial flow meter, is a tool that gauges the mass flow rate of a fluid as it moves through a tube. Rather than measuring the volume of fluid that passes through a specific point per unit time (such as cubic meters per second), the mass flow meter calculates the mass of the fluid passing through that point per unit time (for example, kilograms per second). To determine the volumetric flow rate, one must divide the mass flow rate by the fluid density. This calculation is straightforward when the density of the fluid remains constant. However, if the fluid's density fluctuates due to factors such as temperature, pressure, or composition, the relationship between mass flow rate and volumetric flow rate is more complex. Additionally, if the fluid contains multiple phases (such as a liquid with entrained bubbles), the density can be determined by analyzing the sound velocity dependence on the concentration of the controlled liquid.
Level Measurment
Level measurement is a crucial aspect of the process industry, as even small inaccuracies can result in significant problems such as equipment failure, low-quality output, and even safety hazards. As a result, plant operators rely on a variety of level measurement technologies to ensure precise measurement of gas or liquid levels in tanks or vessels. One of the most widely used and popular devices for level measurement is the level transmitter. This device is designed to provide accurate and reliable measurement of liquid or gas levels in a tank or vessel. The level transmitter works by converting the level measurement into an electrical signal, which can be transmitted to a remote display or control system. Level transmitters can be classified into two broad categories: contact and non-contact types. Contact level transmitters come in direct contact with the liquid or gas being measured and measure the level using mechanical or electrical means. In contrast, non-contact level transmitters measure the level without coming in contact with the liquid or gas being measured and use various techniques such as ultrasonic, radar, or laser to measure the distance between the sensor and the liquid or gas surface. Overall, level transmitters are a critical component of the process industry, ensuring accurate and reliable measurement of gas or liquid levels to prevent accidents and optimize production efficiency.
Flow Measurment
flow control is important parameter in the process plant automation be it of Gas or any other Liquids ,although the type of instrument changes as per the criticallity of the flow control. for simpler non critical application flow can be masured in terms of the volume Ex liters per min . For liquids where there is wide density variation & which would affect the process ,the flow has to be measure with Massflow meter ,where in the density,temperature & even pressure is measures to get the accurate flow example is Natural gas PNG measurment
Pressure Measurment
In engineering, a pressure sensor is a device utilized for measuring the pressure of gases or liquids. Pressure is an expression of the force required to stop a fluid from expanding and is usually quantified as force per unit area. Typically, pressure sensors act as transducers that generate an electrical signal as a function of the pressure imposed on them. These sensors are commonly used for control and monitoring in a vast range of everyday applications, and they can also be employed to indirectly measure other variables, such as fluid or gas flow, speed, water level, and altitude. Pressure sensors can take many forms, with varying technology, design, performance, application suitability, and cost. In fact, it is estimated that there are over 50 different technologies and at least 300 companies producing pressure sensors globally. There is a specific category of pressure sensors designed to measure pressure changes in a dynamic mode to capture very high-speed changes in pressure. For example, these sensors are commonly utilized to measure combustion pressure in an engine cylinder or a gas turbine. Typically, they are manufactured out of piezoelectric materials like quartz. Some pressure sensors are also classified as pressure switches, which turn on or off at a specific pressure level. For example, a water pump can be controlled by a pressure switch that starts the pump when the water is released from the system, reducing the pressure in a reservoir. Therefore, pressure sensors are vital instruments in various engineering applications for ensuring safe and efficient operations.
Temperature sensors are essential components in chemical industries, where temperature control is critical for the quality of the end product. These sensors continuously monitor changes in temperature and provide data for process control and optimization. This research paper focuses on evaluating six different types of temperature sensors based on four parameters: sensor location, accuracy, temperature range, and sensor size. The study concludes that technological temperature sensors are the best option for producing high-quality products. Sensor location refers to where the temperature sensor is installed within the process, such as in the reactor vessel, pipeline, or heat exchanger. Accuracy is a critical parameter as it determines the precision of the temperature measurement. The range of temperature measured is also important as different processes require different temperature ranges. Finally, the size of the temperature sensor is critical for installations where space is limited. The study concludes that technological temperature sensors, such as thermocouples and resistance temperature detectors (RTDs), are the best option for achieving accurate temperature measurements across a wide temperature range. These sensors have a high level of accuracy and can be installed in various locations, making them ideal for monitoring temperature in chemical processes. Additionally, they come in a range of sizes to fit different installation requirements. In summary, temperature sensors play a critical role in chemical industries, and the selection of the right type of sensor is essential for producing high-quality products. Technological temperature sensors, such as thermocouples and RTDs, are the preferred choice due to their accuracy, temperature range, and versatility in sensor location and size.