Why use HART?
Hart Protocol to Quadruple the measurements
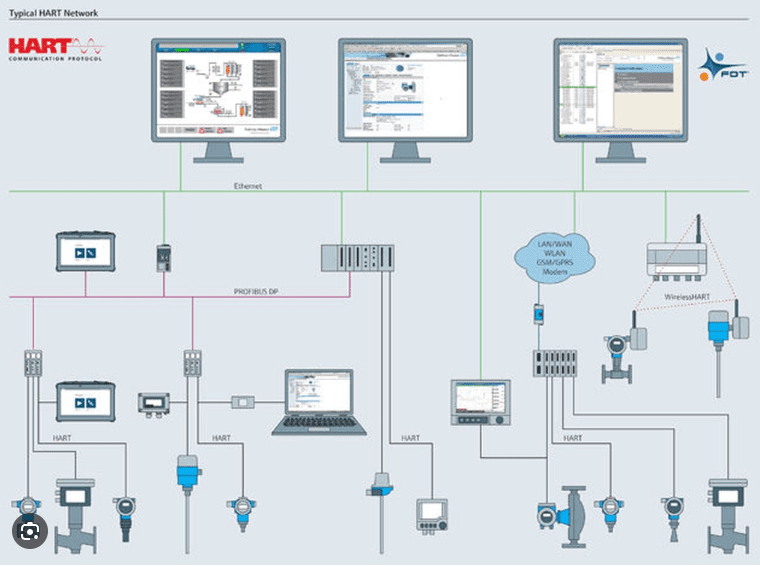
Why use HART? based instruments and hart based analog inputs in plc
Mostly all field instruments can measure just the one singular primary process parameter from the field and transmit the same to plc controller over analog input.
These instruments and Plcs analog instruments you can monitor the critical process upto 4 process variable with one one instrument and one analog inputs .
It’s saves lot of process overheads and mechanical fittings ,plc analog inputs and shielded cables
benefits of using HART protocol
Hart protocol can get 4 parameter reading from the field instrument like mass flowmeter on single pair of instrument cable . with hart protocol user can select which all parameters to select to monitor from multitude of available parameters like flow ,volume ,totalizer , temperature ,Density etc .Traditional means of analog inputs can get only one parameter .all field instruments can measure just the one singular primary process parameter from the field and transmit the same to plc controller over analog input.
These instruments and PLC’s analog instruments you can monitor the critical process up to 4 process variable with one one instrument and one analog inputs .
It’s saves lot of process overheads and mechanical fittings ,plc analog inputs and shielded cables
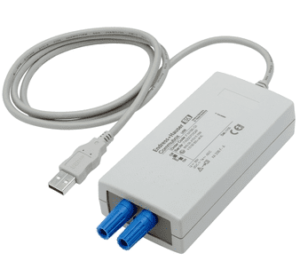
Hart is a hybrid analog+digital communication protocol that enables two-way communication between intelligent field devices and control systems. Its hybrid nature combines the best of both worlds, using the analog signal for the primary process variable and the digital signal for secondary variables, advanced diagnostics, and device configuration.
One of the key benefits of this is its ability to communicate over legacy 4-20 mA analog instrumentation current loops, making it an ideal solution for upgrading existing systems or retrofitting older equipment. These devices can also provide advanced diagnostics, predictive maintenance information, and multiple process variables in a single device, reducing downtime and maintenance costs while improving system reliability.
These devices are easy to commission and manage, thanks to their digital communication capabilities and simple integration into control systems using standard communication protocols like Modbus and OPC. They can also be configured and managed using auxiliary hardware and handheld devices, enabling users to configure and manage these devices in the field.
As a widely adopted industry-standard communication protocol, it offers a comprehensive range of measuring instruments and worldwide service and support options. Partnering with our company can help readers fully exploit the potential of this Communication Protocol in their operations, improving system reliability, reducing downtime and maintenance costs, and increasing overall productivity.
Upgrade your industrial automation system with this Communication Protocol and experience the benefits of its hybrid analog+digital nature, comprehensive range of measuring instruments, advanced diagnostics, intelligent multivariable devices, simple commissioning and device management, simple integration into control systems, auxiliary hardware and handheld, and worldwide service and support. Contact us today to learn more.
HART full form is (Highway Addressable Remote Transducer) is a communication protocol widely used in process plants and industrial automation. It combines analog and digital communication to provide various benefits to process plants. Here are some of the ways process plants benefit from it:
1. Compatibility: it is a backward-compatible protocol that allows existing analog instrumentation to communicate with digital systems. It can be used with both traditional 4-20 mA analog devices and newer digital devices, ensuring compatibility across different generations of equipment.
2. Enhanced Communication: it adds digital communication capabilities to analog devices, enabling two-way communication. This means that in addition to the analog signal, devices can exchange digital information such as process variables, diagnostics, configuration data, and maintenance information. This enhances the level of communication and data exchange between devices and control systems.
3. Remote Configuration and Diagnostics: it enables remote configuration and diagnostics of devices. Plant operators and maintenance personnel can access device parameters, perform configuration changes, and diagnose issues without physically accessing the field devices. This reduces downtime, improves maintenance efficiency, and allows for proactive troubleshooting.
4. Asset Management: it supports asset management functionalities, such as device identification, status monitoring, and predictive maintenance. By continuously monitoring device parameters and diagnostics, plant operators can identify potential issues or deviations from normal operation. This allows for proactive maintenance scheduling, reducing the risk of unexpected equipment failures and optimizing plant performance.
5. Integration with Control Systems: it seamlessly integrates with control systems, distributed control systems (DCS), and programmable logic controllers (PLC). The digital data exchanged through it can be easily incorporated into the control system for monitoring, control, and data analysis. This integration enables tighter process control, improved efficiency, and better decision-making based on real-time data.
6. Increased Efficiency and Productivity: With it, operators can access and analyze device data to optimize process parameters and improve efficiency. Real-time information from field devices helps in identifying bottlenecks, optimizing production, and reducing energy consumption. It also allows for remote monitoring of critical equipment and process variables, ensuring smooth plant operation and minimizing manual intervention.
Overall, it provides process plants with improved communication, increased visibility into device performance, remote configuration and diagnostics, enhanced asset management capabilities, and integration with control systems. These benefits contribute to better operational efficiency, reduced downtime, improved maintenance practices, and overall cost savings for process plants.