Mitsubishi Servo motors & advanced Motion control cards
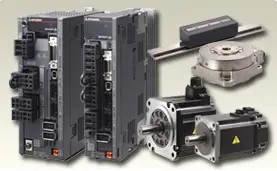
mitsubishi servo motors and drive systems go beyond .customer needs and deliver efficiency and precision in motion control applications .in highly demanding applications ,mitsubishi has motion cards which use optical fibre with proprietary communications protocls like SSCNET to avoid the effects of electrical noise.
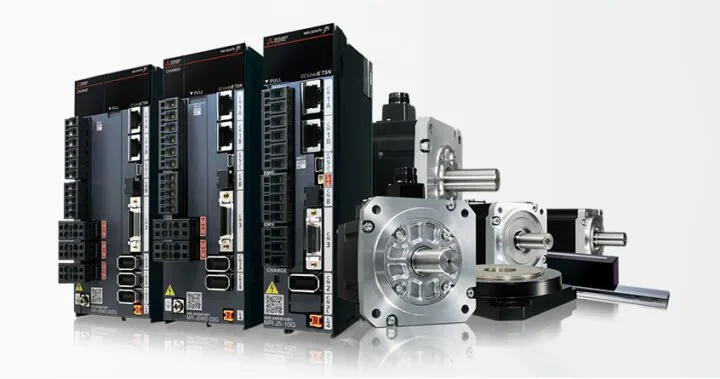
Mitsubishi servo motors can be operated through pulse control, analog inputs, and using a motion card with SSCNET.
1. Pulse Control:
Pulse control involves sending pulses to the servo motor to control its position, speed, and direction. The motor’s position and motion parameters are determined by the specific pulse signals it receives. Pulse control enables precise positioning and motion control by sending dedicated pulse signals based on desired parameters.
2. Analog Inputs:
Servo motors can be operated using analog inputs, where control signals are derived from analog voltage or current signals. These signals are typically generated by sensors or potentiometers. By adjusting the analog input signal, the speed and position of the servo motor can be controlled. Analog inputs provide continuous control, allowing for smooth and accurate operation.
3. Motion Card using SSCNET:
Mitsubishi servo motors can be operated through a motion card utilizing SSCNET (Servo System Controller Network). SSCNET is a high-speed serial communication network developed by Mitsubishi Electric for motion control applications. A motion card or controller communicates with the servo drives via SSCNET, providing control signals for position, speed, and other motion parameters. This setup allows for precise coordination and integration of multiple axes and other motion control devices.
These three methods—pulse control, analog inputs, and motion card with SSCNET—provide different options for operating Mitsubishi servo motors, catering to specific application requirements and control preferences.
Seamlessly Powering All Machines: Mitsubishi’s MELSERVO-JE Systems for Reliable Performance and User-Friendly Operation.
Mitsubishi Servo drive features
Advanced One-Touch Tuning
gains are adjusted with one-touch ease without a personal computer.
Tolerance against Instantaneous Power Failure
The instantaneous power failure tough drive function and the large capacity capacitor reduce machine downtime.
Absolute Position Detection System 
Absolute position detection system can be easily configured with MR-JE-B servo amplifier.
Built-in Positioning Function 
MR-JE-A has a built-in positioning function, enabling positioning operation with point table method, etc. Equipped with advanced functions such as simple cam and mark detection.
SSCNETIII/H 
MR-JE-B is compatible with 150 Mbps full duplex high-speed optical network SSCNETIII/H, achieving high-response system.
Fast and Accurate
The dedicated engine enables speed frequency response of 2.0 kHz, shortening the tact time.
High Resolution Encoder
The servo motor is equipped with 131072 pulses/rev (17-bit) high-resolution encoder, achieving high accuracy.
Energy Conservation
The large capacity main circuit capacitor allows the regenerative energy to be used effectively, reducing energy consumption.
Compliance to Global Standards
Global servo, MR-JE series, complies with global standards as standard.
Sink and Source Connections
Command pulse input and digital input/output are compatible with both sink and source type connections.
Global Support
FA Centers located throughout the world provide attentive services to support users.
Servo-controlled systems offer several advantages over mechanical systems, making them preferable in many applications. Here are some reasons why servo-controlled systems are considered superior:
1. Precision and Accuracy: Servo-controlled systems provide exceptional precision and accuracy in controlling motion. Servo motors can achieve high resolution, allowing for precise positioning and movement control. This accuracy is crucial in applications where tight tolerances and repeatable motion are required.
2. Speed and Performance: Servo-controlled systems can achieve high speeds and rapid acceleration/deceleration rates. They offer excellent dynamic response, enabling quick and precise movements. This makes them suitable for applications that require fast and responsive motion, such as robotics, CNC machining, and automation.
3. Flexibility and Versatility: Servo-controlled systems are highly flexible and adaptable. They can be easily programmed and adjusted to perform various tasks and adapt to changing requirements. By changing control parameters, servo systems can handle different loads, speeds, and motion profiles, offering versatility in different applications.
4. Closed-Loop Control: Servo systems operate in a closed-loop control configuration, meaning they continuously monitor and adjust the motor’s position, velocity, and torque based on feedback from sensors. This feedback loop enables precise control and ensures that the system maintains the desired motion and position accurately, even in the presence of external disturbances or variations.
5. Smooth and Controlled Motion: Servo motors provide smooth and controlled motion profiles. They can follow complex motion paths with minimal vibration, jerk, or backlash, resulting in smoother operation and reduced wear on mechanical components. This is particularly advantageous in applications that require precise and smooth motion, such as robotic arms and automated machinery.
6. Integration and Connectivity: Servo systems often offer advanced connectivity and integration capabilities. They can be easily integrated into complex control architectures, such as industrial automation systems or robotic control networks. Additionally, servo systems often support various communication protocols, enabling seamless integration with other devices and control systems.
7. Monitoring and Diagnostics: Servo systems typically provide monitoring and diagnostic features. They can measure and report data such as motor temperature, current consumption, and position feedback. This information allows for real-time monitoring, predictive maintenance, and troubleshooting, improving system reliability and uptime.
While mechanical systems may still be suitable for simpler applications, servo-controlled systems excel in scenarios that require precise motion control, high performance, and adaptability. Their ability to deliver accurate, fast, and flexible motion makes them the preferred choice in many industrial and automation applications.